ONE GOLDEN LANE
Can we create new, world class office space through optimised reuse of material proposed for demolition?
Location: Barbican
Status: On Site
Client: Castleforge
Architect: Hawkins Brown
:
Structural Design Brief
Refurbishment of existing office building to Grade A office space.
Addition of four new storeys with core rearrangements and extensions to north and south facades.
Optimisation of reuse of steel identified for demolition- reusing 40 tonnes of steel.
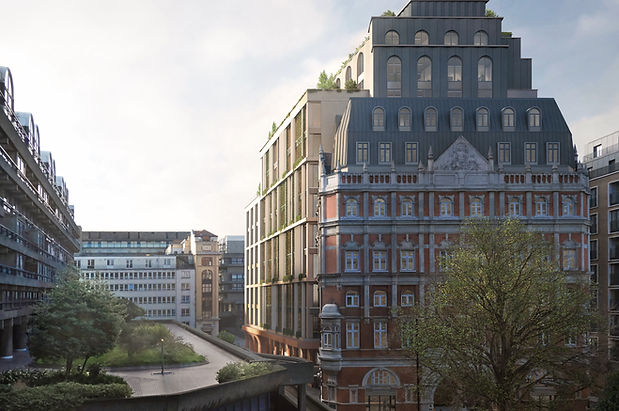
Located near to The Barbican, London, the existing Grade II listed building was built in 1896 had a fourth floor added around 1912. In the 1990s, the building was largely demolished and rebuilt, with the retention of masonry façade, heritage staircase and Victorian vaults to the perimeter. This complex history, in a sensitive location, required surgical cuts to be made into the 1990’s steel frame, to enable the buildings potential.
The development will refurbish and extend the existing office building, with the addition of four new storeys, extensions to the North and South façades and core optimisation, providing new Grade A office space within the City of London. To maximise use of space in the development, the stability system is to be reconfigured, removing existing steel bracing and providing new steel bracing in central locations that are both more efficient and work with the proposed layouts.
Through more sophisticated analysis techniques than would have been available during the 1990’s redevelopment, we were able to assess the steel bracing and historic masonry as a single system, avoiding the need for any foundation enhancement even with the increased massing.
The client and team have high sustainability aspirations and we are adopting a Net-Zero approach. When developing the design for this refurbishment and extension, we wanted to optimise the reuse of the material proposed to be removed in the demolition. To do this, we developed an algorithm that identifies the opportunities for reuse of steelwork within the proposed four storey extension and infill, enabling nearly 25% of the steel being removed to be reused in the development- some 40 tonnes - through section substitution and augmentation methods. This approach enabled a lower carbon impact than would have been required to deliver the same area with a timber frame.
Renders courtesy of Secchi Smith